Introduction
The air release valve, or air valve, is one of the most important components of fluid transmission systems and facilities, playing a crucial role in the efficiency and safety of these systems. In fluid transmission and water supply networks, trapped air can cause serious issues such as reduced water flow, vibrations, annoying noises, and even equipment failure. Air release valves are designed to effectively and safely discharge the trapped air in pipes, preventing such problems.
These valves play a vital role in various applications, including heating systems, water supply, and diverse industries. In addition to preventing flow disturbances, air release valves help extend the system’s lifespan and reduce maintenance costs. Given the importance of this component in different systems, understanding its types, functions, and benefits can aid in the optimal selection and use of this product.
In this article, we will thoroughly examine air release valves, their types, how they function, and their applications. Furthermore, important tips for installing and maintaining these valves will be provided to ensure that your fluid transmission networks operate as efficiently as possible. Stay tuned with Beniz Tajhiz’s blog…
Air Release Process
An air release valve acts as a vent designed to discharge trapped air in the pipes. The operation of these valves is based on the difference in density between water and air. When water enters the valve and contains air, the internal mechanism of the valve functions to release the trapped air. This process prevents abnormal pressure and blockages in the water flow. The overall operation of the air release valve is as follows:
- Air Accumulation Detection: When air collects at a point in the pipe, the internal pressure of the system changes. This pressure change is detected by the air release valve.
- Valve Opening: As the air pressure inside the pipe increases, the air release valve automatically opens, and the internal vent moves upward to discharge the air.
- Air Discharge and Valve Closure: Once the trapped air is released and water reaches the valve, the internal vent moves downward and closes the air discharge path to prevent water from escaping.
This automatic operation ensures that the water flow in the system remains uniform and uninterrupted, especially in irrigation systems where maintaining a continuous flow and preventing blockages is of utmost importance.
Types of Air Release Valves
Air release valves can be categorized into different types based on their operation and material composition. Each type has its own specific features, advantages, and disadvantages, which are selected based on the system’s needs and operating environment. In this section, we will explore the various types of air release valves in terms of their operation and material.
1. By Operation:
- Automatic Air Release Valves: These valves automatically discharge air from the system without requiring manual intervention, making them an ideal choice for systems that need continuous monitoring.
- Advantages: Ease of use, automatic operation, and reduced maintenance needs.
- Disadvantages: Higher cost compared to manual valves, more prone to failure.
- Manual Air Release Valves: These valves require manual intervention to release air and are commonly used in systems that need less frequent air removal and manual control.
- Advantages: Lower cost and precise manual control.
- Disadvantages: Requires continuous monitoring and is susceptible to human error.
2. By Material:
- Metal Air Release Valves: These valves are typically made from materials such as brass, steel, or cast iron, offering high resistance to pressure and temperature.
- Advantages: High durability, corrosion resistance, and suitable for harsh conditions.
- Disadvantages: Heavier and more expensive.
- Plastic Air Release Valves: Made from polymers, these valves are generally used in lighter and lower-pressure systems.
- Advantages: Lightweight, cost-effective, and resistant to chemical corrosion.
- Disadvantages: Lower resistance to pressure and temperature, shorter lifespan compared to metal valves.
3. Combination Valves:
Some valves are a combination of metal and plastic, where the internal components are made of plastic and the body is made of metal. This combination ensures that the valves are both highly durable and lighter in weight and cost-effective.
Selecting the right type of air release valve depends on several factors, including environmental conditions, system pressure and temperature, and budget. Understanding the pros and cons of each type helps in making the best choice for your specific needs.
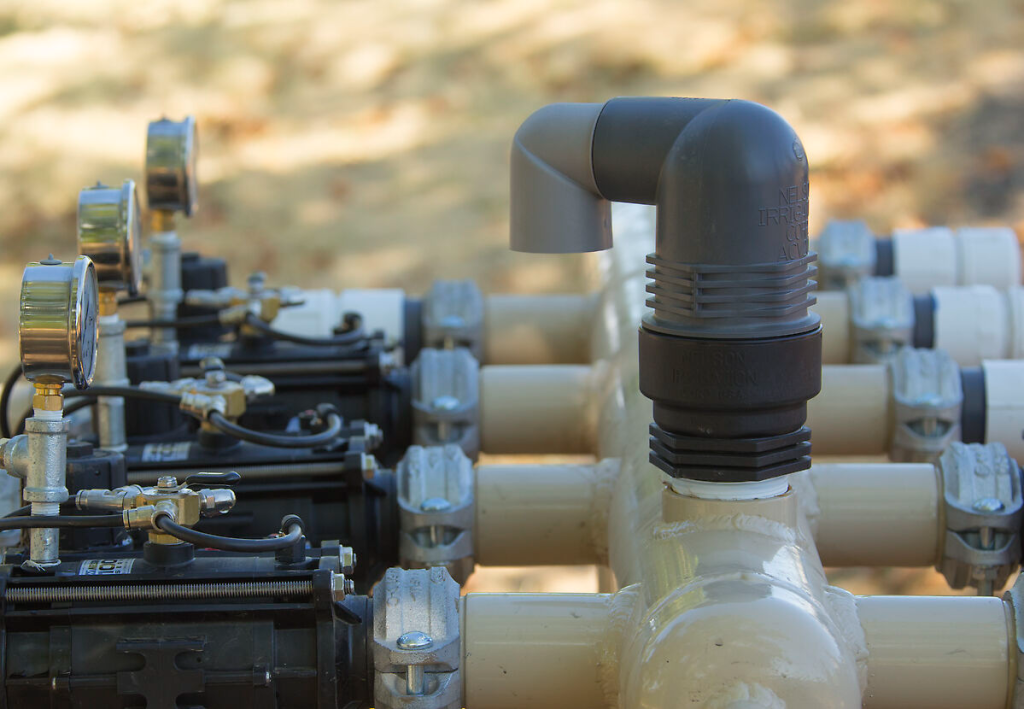
Applications of Air Release Valves
Air release valves, also known as air vent valves, are used in a wide range of industries and systems, especially where the accumulation of air can disrupt system performance. These valves play a crucial role in maintaining system efficiency and safety, and their use is widespread in various industries. In this section, we will explore the applications of air release valves in different industries and systems.
- Water and Wastewater Industries:
In water supply and wastewater systems, air release valves prevent the accumulation of air in pipelines, which can reduce flow and pressure. These valves help improve system efficiency and prevent the formation of air pockets in the pipes. - Heating and Cooling Systems:
In heating and cooling (HVAC) systems, air accumulation can reduce heat transfer and lower system efficiency. Installing air release valves in these systems improves efficiency and extends equipment lifespan. - Oil and Gas Industries:
In oil and gas pipelines, the presence of air can create gas pockets and disrupt liquid flow. Air release valves in these systems act as a critical tool for maintaining stable flow and preventing potential system failures. - Irrigation Systems:
In irrigation systems, particularly drip and sprinkler irrigation, the presence of air can cause nozzle blockages and reduce system efficiency. The use of air release valves in these systems enhances water distribution and reduces the likelihood of blockages. - Industrial Facilities:
In industrial facilities that deal with various liquids and gases, air release valves are used to maintain optimal system performance and prevent potential damage caused by air accumulation. - Power Plants:
In power plants, especially steam power plants, air accumulation in fluid transmission networks can reduce production efficiency and pose safety hazards. Air release valves in these systems act as a preventive measure to maintain efficiency and safety.
Air release valves have a wide range of applications in various industries and systems, playing a key role in maintaining system efficiency and safety. Proper selection and installation of these valves can improve performance and reduce long-term maintenance costs.
Difference in Air Venting Process in Drip and Sprinkler Irrigation Systems
Drip and sprinkler irrigation systems are two common methods for irrigating agricultural fields and green spaces. Both systems are designed to distribute water evenly, but due to structural and operational differences, the air venting process in these systems varies. In this section, we will examine the differences in the air venting process in drip and sprinkler irrigation systems.
- Drip Irrigation System:
In drip irrigation systems, water is delivered directly to the roots of plants through thin pipes and small nozzles. These systems, due to the low pressure and drop-by-drop flow of water, are more prone to air accumulation. The presence of air in the pipes and nozzles can cause blockages and reduce the efficiency of the system. In such systems, air release valves must be regularly installed to continuously vent trapped air and prevent nozzle blockages. Additionally, due to the small diameter of the pipes, even a small air bubble can have a significant impact on the water flow. - Sprinkler Irrigation System:
In sprinkler irrigation systems, water is directed under pressure to spray nozzles (sprinklers) and distributed in fine water droplets over the ground. These systems, due to the higher pressure and continuous water flow, are less prone to air accumulation. However, when the system is turned on and off, air may enter the pipes. In these systems, air release valves are mostly installed at elevated points to vent trapped air and ensure the proper functioning of the sprinklers. - Pressure and Water Volume:
One of the key differences between drip and sprinkler irrigation systems is the pressure and volume of water. In drip systems, which operate at lower pressures, air can quickly enter the pipes and significantly affect water flow. In contrast, in sprinkler systems that operate at higher pressures, trapped air usually exits the system quickly, but regular air venting is still necessary. - Key Locations for Installing Air Release Valves:
In drip irrigation systems, air release valves are installed near the nozzles and at the end of the lines to prevent any blockages. In sprinkler systems, air release valves are mainly placed at higher points and near the sprinklers to allow trapped air to escape easily.
The air venting process in drip and sprinkler irrigation systems differs due to the structural differences and operating pressures of these systems. Understanding these differences and the proper use of air release valves can help improve performance and reduce issues in these systems.
Installation and Maintenance of Air Release Valves
Proper installation and maintenance of air release valves are essential for the optimal performance and longevity of liquid transfer and irrigation networks. These valves should be installed in suitable locations to correctly release air from the system. Additionally, regular maintenance of these valves prevents potential issues. In this section, we will cover the key points for installing and maintaining air release valves.
1. Installation Location:
- Elevated Points: Air release valves should generally be installed at elevated points and areas where the slope of the land changes, as air tends to accumulate in the upper parts of the pipes. Installing them at elevated points allows trapped air to easily exit the system.
- Near Sprinklers and Nozzles: In irrigation systems, especially drip irrigation, air release valves should be installed near the nozzles and sprinklers to prevent blockages.
- End of Lines: At the end of liquid transfer lines, air accumulation is more likely. Installing air release valves in these points prevents air from entering the system.
- Standard Distances: If the liquid transfer network has long lines, an air release valve is typically installed every 500–600 meters to prevent water flow issues. In long horizontal pipes, an appropriate slope is created to move air towards elevated points, where it is then vented.
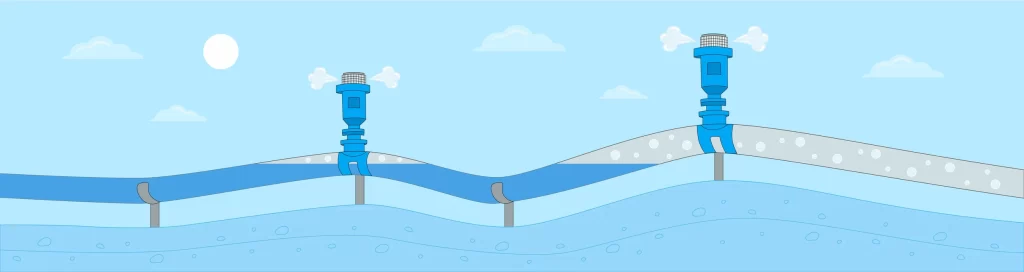
2. Vertical Installation:
The air release valve should be installed vertically to properly vent the air. Vertical installation allows the valve to effectively detect and release air from the system.
3. Distance from Sensitive Equipment:
Air release valves should be installed in such a way that they are far from sensitive and critical equipment. This prevents any potential impact from leaks or valve malfunctions on the equipment.
4. Regular Maintenance:
- Performance Check: Periodically check the performance of the air release valves to ensure they are venting air properly.
- Cleaning: In environments with a lot of particles and debris, air release valves may become clogged. Regular cleaning of these valves improves performance and prevents malfunction.
- Replacement of Worn Parts: Internal parts of air release valves may wear out over time. Timely replacement of these parts prevents serious failures.
5. Proper Insulation:
In areas where freezing is possible, air release valves must be well-insulated to prevent freezing and damage to the valves.
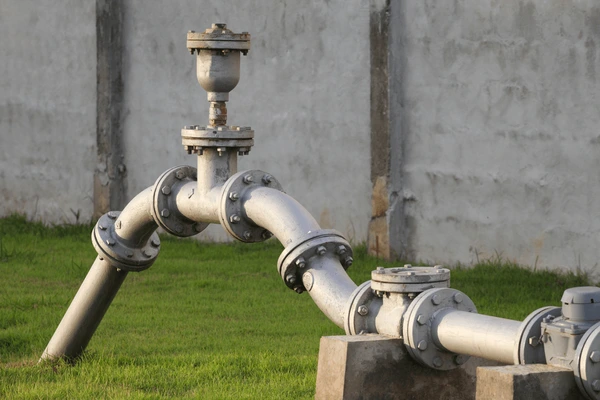
Proper installation and maintenance of air release valves are crucial, as they can reduce issues caused by air accumulation and increase system efficiency. Paying attention to installation locations, regular inspections, cleaning, and replacing parts extends the lifespan of these valves and the liquid transfer network.
?How to Ensure the Proper Functioning of Air Vent Valves
Ensuring the proper functioning of air vent valves is crucial to maintaining system efficiency and preventing issues caused by trapped air. Regular inspection and performance testing of valves can prevent costly failures and reduced system productivity. In this section, we’ll cover key points to help ensure that air vent valves are working correctly.
1. Visual Inspection:
- Leak Detection: Regularly inspect air vent valves for any leaks. A leak may indicate a malfunction or improper valve operation.
- Blockage: Ensure that the valves are not blocked by debris. Suspended particles in the system can clog the valve and reduce its effectiveness.
2. Performance Testing:
- Manual Test (for Manual Valves): If using manual valves, periodically open them to check their functionality. Ensure that the valve opens and closes smoothly and properly vents the air.
- Automatic Test (for Automatic Valves): For automatic valves, you can test the valve’s performance by altering system pressure. If the valve reacts properly to pressure changes and releases air, it is functioning correctly.
3. Using Pressure Gauges:
- Install Pressure Gauges: Installing pressure gauges near air vent valves can help you monitor system pressure. A sudden drop in pressure may indicate the presence of trapped air, which should be vented immediately.
4. Regular Maintenance Program:
- Scheduled Maintenance: Create a regular maintenance schedule for checking and testing air vent valves. This should include periodic inspections and cleaning of the valves.
- Record Keeping: Keep records of valve performance over time to identify potential failure patterns or performance degradation, allowing for preventive measures.
5. Staff Training:
- Employee Training: Employees responsible for valve maintenance and supervision should be trained to identify issues and test valve functionality correctly. Proper training can enhance overall system performance.
Ensuring proper functioning of air vent valves through regular inspections, performance tests, and using tools such as pressure gauges can help maintain system efficiency and prevent issues caused by air accumulation. Having a regular maintenance plan and training staff also plays an important role in this process.
Consequences of Improperly Functioning Air Vent Valves in Irrigation Systems
The proper functioning of air vent valves in irrigation systems is essential for maintaining system efficiency and preventing damage to equipment. If these valves fail to operate correctly, various problems can arise, leading to reduced system efficiency or even serious damage. This section explores the potential consequences of malfunctioning air vent valves in irrigation systems.
1. Reduced Water Pressure and Flow
Air trapped in the pipes can cause a significant reduction or complete stoppage of water flow. This is particularly problematic in drip irrigation systems, as it can result in poor or uneven water distribution, lowering the system’s efficiency.
2. Airlocks
Trapped air in the pipes can create airlocks, blocking the proper flow of water. This issue may require complex and expensive repairs to remove the airlock and restore the system’s functionality.
3. Equipment Damage
Continuous air buildup can lead to abnormal pressure in the pipes and equipment. This excess pressure may cause pipe breakage, joint failure, and other equipment damage, resulting in costly repairs.
4. Shortened System Lifespan
Improper valve function and air accumulation can cause internal pressure build-up, reducing the lifespan of the system. Equipment exposed to abnormal pressure conditions will experience wear and tear faster than expected.
5. Uneven Water Distribution
In sprinkler systems, trapped air can cause uneven water distribution, leading to areas of the field being over- or under-watered. This imbalance can result in poor crop growth or landscaping issues.
6. Increased Maintenance Costs
Without properly functioning air vent valves, frequent maintenance and repairs will be necessary. This can increase the operational costs of running the irrigation system.
7. Environmental Hazards
If air buildup damages the system, leading to water leakage, it may cause environmental issues, especially in sensitive areas where water conservation is crucial.
Malfunctioning air vent valves can have serious consequences for irrigation systems, from reduced water pressure to equipment damage and increased operational costs. Regular inspection and maintenance are crucial to avoid these issues and maintain system efficiency.
Benefits of Using Air Vent Valves
Air vent valves play a vital role in maintaining the efficiency and performance of irrigation systems and liquid transfer networks. By releasing trapped air from the pipes and equipment, they prevent issues like pressure reduction, blockages, and equipment damage. In this section, we’ll explore the benefits of using air vent valves.
1. Maintain Constant Water Pressure and Flow
One of the key benefits of using air vent valves is maintaining constant water pressure and flow in irrigation systems. Air accumulation in pipes can reduce pressure, affecting the system’s overall performance. Air vent valves effectively release trapped air, ensuring smooth water flow.
2. Prevent Equipment Damage
Trapped air can lead to excess pressure in the system, which may damage equipment such as pipes and connections. Air vent valves significantly reduce this risk by releasing the air, preventing equipment breakage, and extending the lifespan of the system.
3. Reduce Energy Consumption
When air is trapped in the pipes, pumps and other equipment have to work harder to maintain the required pressure. By venting the air, energy consumption is optimized, reducing operational costs.
4. Improve Irrigation System Performance
In both drip and sprinkler irrigation systems, uniform water distribution is essential for plant growth. Using air vent valves prevents blockages in nozzles and sprinklers, ensuring efficient and uniform water distribution across the field, leading to improved crop yields.
5. Minimize Environmental Risks
By preventing water leakage and optimizing water use, air vent valves help in the efficient management of water resources. This is especially critical in water-scarce regions where conservation is a priority.
6. Reduce Maintenance Costs
By minimizing the chances of breakdowns and blockages, air vent valves lower the frequency of maintenance and repair requirements, resulting in cost savings for the system operator.
7. Increase System Lifespan
Due to reduced internal pressure and prevention of equipment damage, the use of air vent valves extends the overall lifespan of irrigation systems and liquid transfer networks, reducing long-term costs and enhancing system productivity.
Using air vent valves in irrigation systems and liquid transfer networks offers numerous benefits, including maintaining constant water pressure, preventing equipment damage, reducing energy consumption, and improving system performance. These valves play a crucial role in optimizing the functionality and longevity of irrigation systems.
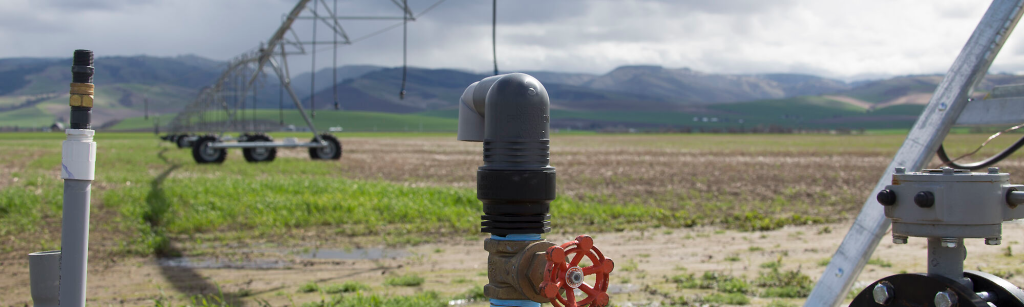
Conclusion
In conclusion, the use of air vent valves is highly recommended as an essential and effective measure in irrigation systems and liquid transfer networks. Air vent valves are critical components that help maintain the efficiency and proper operation of these systems. By releasing trapped air in the pipes, they prevent pressure reduction, blockages, and equipment damage.
Given the importance of air vent valves in system longevity and cost reduction, careful attention should be given to their design, installation, and maintenance.
We hope this article has been helpful. If you have any questions or comments, feel free to leave them below. Thank you for your continued support!